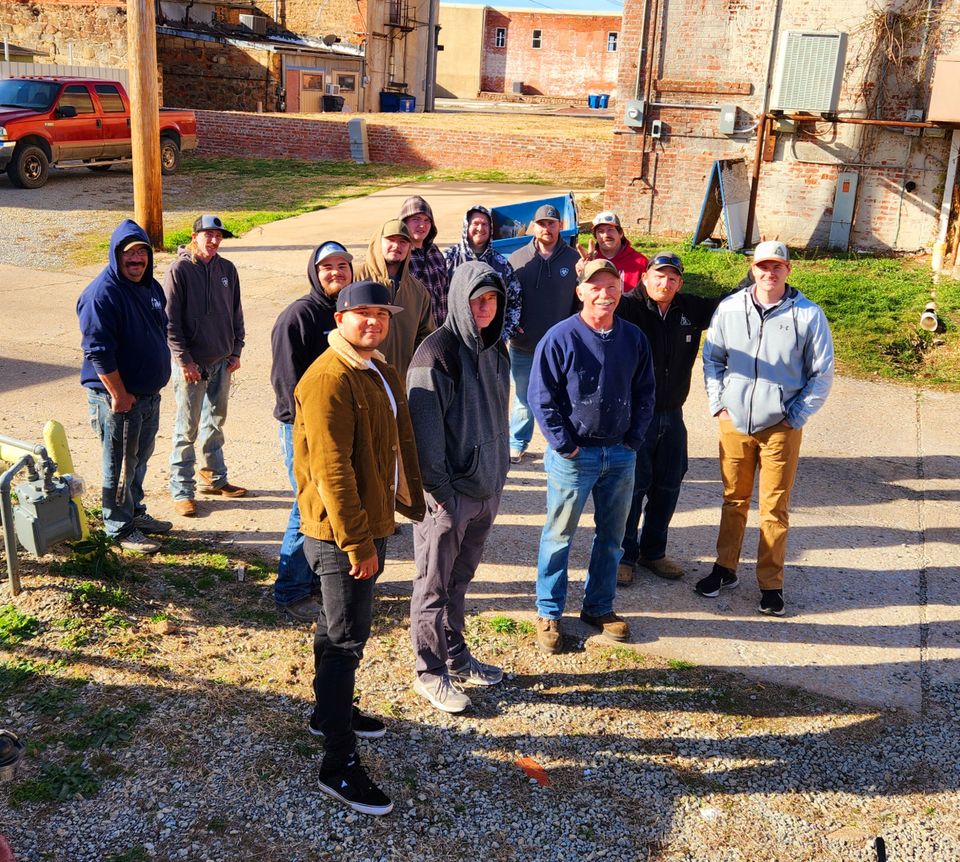
The Ultimate Guide to Operator Qualification (OQ) Training
Ensuring Safety and Compliance
Operator Qualification (OQ) training is a critical component of workplace safety, particularly for industries involving high-risk operations like pipelines, utilities, and hazardous material handling. At 25/8 Safety, we provide comprehensive OQ training tailored to meet regulatory standards while empowering your team with the skills to operate safely and efficiently.
Operator Qualification (OQ) training is a critical component of workplace safety, particularly for industries involving high-risk operations like pipelines, utilities, and hazardous material handling. At 25/8 Safety, we provide comprehensive OQ training tailored to meet regulatory standards while empowering your team with the skills to operate safely and efficiently.